一、风门气动控制装置:自动化通风的核心执行单元
(一)气动风门控制装置 矿用风门气动闭锁装置技术架构与工作原理
风门气动控制装置以压缩空气为动力源,采用 "传感 - 控制 - 执行" 的闭环控制逻辑。其核心由传感器模块(红外 / 微波感应)、气动控制箱(含 PLC 与电磁阀)、气动执行缸三部分组成。当传感器检测到人员或车辆接近时(红外感应≥3 米,微波感应≥5 米),控制箱内电磁阀切换气路,压缩空气推动气缸活塞杆伸缩,通过连杆机构带动风门在 1.5 秒内完成开启;目标通过后,控制箱按预设延时(3-10 秒)关闭风门,整个过程实现无人化操作。
该装置的技术创新在于将无压

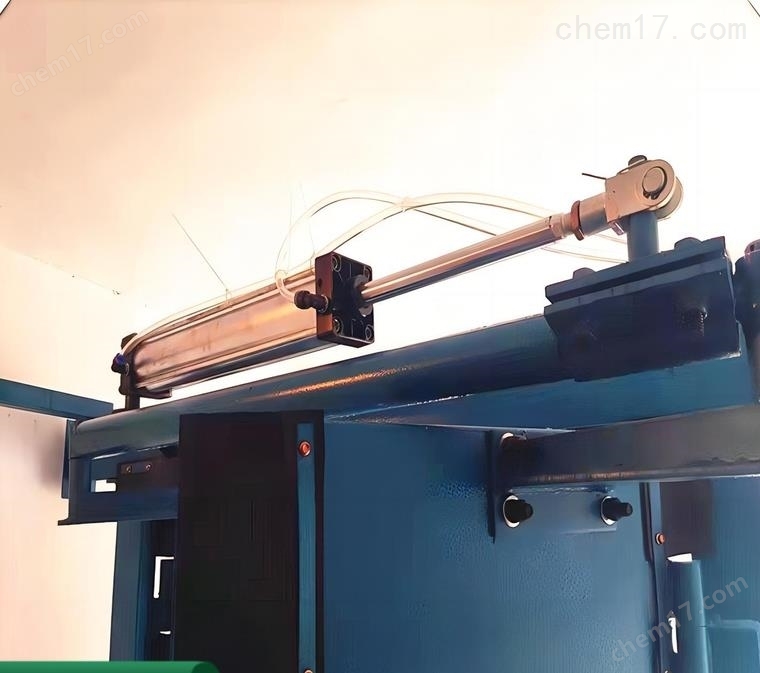
平衡原理与气动驱动结合:双扇风门呈 180° 反向布置,利用风压在轴心上形成力矩平衡,使开启力从传统手动风门的 800-1000N 降至 300N 以下,配合 500-800N 的气缸推力,即使在 2000Pa 风压环境下也能轻松启闭,解决了传统风门 "开启费力、关闭不严" 的痛点。 (二)气动风门控制装置 矿用风门气动闭锁装置安全特性与环境适配
纯气动驱动模式赋予装置本质防爆特性,无需电力即可运行,从根源上消除电火花隐患,满足高瓦斯矿井的安全要求。某瓦斯突出矿井应用数据显示,装置投用后因风门问题引发的瓦斯超限次数同比下降 65%。其应急可靠性同样关键 —— 在停电或电控系统故障时,储气罐内的压缩空气可维持风门至少 48 小时的正常启闭,为井下人员撤离提供 "生命通道"。
在结构设计上,装置采用模块化布局,金属部件选用 304 不锈钢或镀锌处理,管路使用防爆胶管,控制箱达到 IP54 防护等级,能在湿度 95%、粉尘浓度 800mg/m³ 的环境中稳定运行,适配主要风巷、采区巷道、掘进工作面等不同场景。
二、自动风门闭锁装置:防止风流短路的关键屏障
(一)双重闭锁机制与技术突破
自动风门闭锁装置的核心功能是实现两扇风门的互锁控制,其创新在于 "机械 + 气动" 的双重闭锁设计:当一扇风门开启时,气动缸通过连杆机构对另一扇风门施加≥500N 的闭锁力,同时机械锁舌插入锁孔形成刚性固定,确保任意一扇风门开启角度超过 5° 时,另一扇 闭锁。这种双重闭锁机制较传统机械闭锁响应速度提升 40%,闭锁可靠性提高 65%, 杜绝两扇门同时开启导致的风流短路。
装置内置风压传感器,当检测到两侧风压差超过 1500Pa 时,会自动增强闭锁力(最大可达 800N),抵抗风压波动对风门的冲击。某矿通风科实测数据显示,该装置在 2000Pa 正负风压交替变化中,闭锁失效概率低于 0.01%,远优于行业标准要求。
(二)智能化升级与联动控制
现代自动风门闭锁装置已从单一机械闭锁升级为智能联动系统。通过接入矿井 PLC 监控网络,可实时上传闭锁状态(锁定 / 解锁)、闭锁力数值、风压数据等信息至地面调度中心,管理人员通过三维可视化平台即可远程监控全矿闭锁装置运行情况。当某区域风门出现异常开启时,系统自动触发相邻闭锁装置增强锁定,并发出声光报警,将通风异常处置效率提升 70% 以上。
部分 型号还集成故障预警功能:当气压过低(<0.4MPa)或管路漏气时,装置立即发出声光报警,并将故障信息推送至维修人员手机终端,使平均故障排查时间从 45 分钟缩短至 12 分钟。
三、协同工作模式与应用效益
(一)一体化系统集成方案
在实际应用中,风门气动控制装置与自动风门闭锁装置通常采用一体化设计:气动控制装置负责风门的自动启闭,闭锁装置则实时监控风门状态并执行互锁控制,二者通过控制箱内的逻辑阀实现数据交互。当气动控制装置接收到开启信号时,同步向闭锁装置发送 "解锁" 指令;风门开启过程中,闭锁装置持续监测另一扇风门的状态,防止误动作。这种协同工作模式使风门系统的可靠性提升至 99.9%。
某大型煤矿的应用案例显示,一体化系统投用后,每月通风异常次数从 12 次降至 1 次以下,矿车通过风门的等待时间从 1.5 分钟缩短至 15 秒,单班运输效率提升 35%,年节约通风能耗约 120 万元,综合投资回收期仅 14 个月。
(二)多场景适配与行业实践
在高瓦斯矿井的采区巷道,装置采用 "气动控制 + 闭锁联动 + 瓦斯传感器" 的三重保障模式:当瓦斯浓度超过 1.0% 时,闭锁装置自动锁定风门并启动反风程序;在掘进工作面,针对空间狭窄、粉尘大的特点,选用紧凑型气缸与微波感应组合,配合闭锁装置的抗振动设计,确保在爆破作业后仍能正常工作;在主要风巷,则加强闭锁装置的抗风压能力,将最大闭锁力提升至 1000N,适应大流量通风需求。
山西某矿的智能化升级实践颇具代表性:该矿将 89 组风门的气动控制与闭锁装置全部接入 5G 工业环网,通过 AI 算法分析风门启闭频率、闭锁力变化与瓦斯浓度的关联关系,提前 20-30 分钟预测通风异常,使瓦斯超限预警准确率达 92%,为智慧矿山建设提供了关键数据支撑。